Garments
Ordering process
1. Placing your order
We can assist (email works best) with building your order, including but not limited to: providing sizing, garment and color recommendations. If you have an existing account with us, we're here to help finalize pricing and any other details. Please let us know if you're needing your printed goods by a certain date, and we can see what's possible. Refer to Pricing Policy for more information on RUSH orders. *Minimum order quantity: 10*
2. Quote finalization and Payment
An order summary outlining the costs is sent via email. Upon approval, payment is processed, securing the order and signaling to us your intent to proceed. Art graphics are sent at this time. Please note, estimates are valid for 60 days, after which they will expire and need to be re-created.
3. Digital Proof Creation
The Art Department crafts a detailed digital proof based on your submitted design. This step involves translating your submitted files into digital renderings of the final printed product. Please note, our proofs are *not* to scale, but rather, show a representation of placement and ink colors with specific print sizing and measurements detailed.
4. Proof Approval and Garment Sourcing
You will receive digital proof(s)for approval. Once confirmed, we'll source the garments for proceeding. This stage ensures all materials are on hand and approved before production begins.
6. Production Queue
With materials sourced, the order is placed onto the production schedule. This is typically by the third business day from initial order placement. Our full turnaround lead time for garment orders can vary throughout the year, most typically being around 2 weeks. During busier times, this lead time can extend further out if our presses are fully booked.
7. Production, Quality Assurance, and Shipping
Printing production begins, followed by rigorous quality checks to ensure each item matches the approved proof. From there, the order is packaged up and you will be notified upon completion (pickup, shipping -default is UPS, or local delivery).
Please note that when your job is finished your screen is reclaimed. We do not save screens. Quick tip! If placing a future reorder, we do keep all of your artwork and past orders on file for quick access, so no need to resend.
Standard Garment Ink Colors
Below are the ink colors we offer at no additional charge. If going with a custom color for us to match, this will involve a $15 Ink mixing fee.
If you'd like to use our softer water-based ink options, this will involve 25¢ per color per item per location. More on ink types further below.
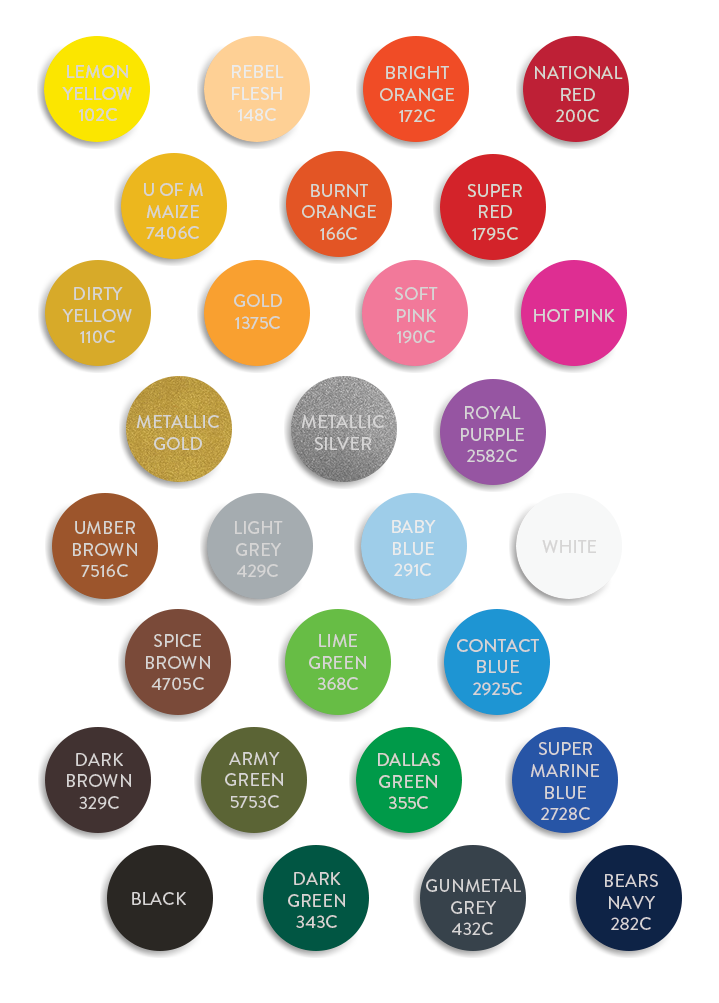
Garment Ink types & Printing Techniques
Standard Plastisol Ink
Plastisol is the standard, less-expensive ink for screen printing. It is made with plastic (polyvinyl chloride, better known as PVC.) This type of ink sits on top of the garment; it doesn't soak in. Because of this, plastisol ink will always produces a bright print, which can feel thick and heavy and allow less breathability than a print with water-based ink.
We can, however, use soft-hand additive upon request that will thin the ink for printing with a lighter and softer feel.
Note: color opacity will subsequently reduce when using soft-hand additive.
Water Based Inks (+$)
Water-based ink is a high-end ink commonly used in retail printing, that is often more eco-friendly. The brightness level of a water-based print can range from very bright to somewhat faded, depending on the fabric of the garment it's printed on. Printing light colors on dark garment can get tricky, so please inquire if this is something you're interested in.
For example, on a 100% cotton t-shirt, your graphic will print very bright and vibrant. But if printed on a cotton/polyester blend or tri-blend, it might come out more toned down. Water-based ink will leave your shirt with an incredibly soft and much more breathable print than any other ink type. Since the ink soaks into the shirt's fabric, it can't be felt after first laundering.
Specialty Inks
We offer puff, fluorescent and GID garment inks. Please inquire for more information if interested.
Spot Color
Spot color process is a method used where designs are broken down into individual color components and printed using solid colors without gradients. This method is ideal for designs with fewer than six colors and works best with vector files like Adobe Illustrator files.
Spot color process is particularly effective for achieving vibrant prints on dark garments, as it allows for a white underbase that makes the colors printed on top bright and vivid.
This method can be cost-effective, especially for designs with one to four colors. However, for more complex designs, other methods like CMYK or simulated process printing might be more suitable.
CMYK
The CMYK (Cyan, Magenta, Yellow, and Black) method in screen printing is widely used to replicate full-color images on light-colored backgrounds. The inks used in CMYK screen printing are semi-transparent, allowing colors to overlap and create a wide variety of shades. This method is best suited for white or very light-colored garments, as the inks are translucent and will not show up on dark garments.
Simulated Process
Simulated process printing involves blending ink colors using halftones to create complex hues and shades that would be unfeasible using spot colors alone. Simulated process can be more expensive than traditional process printing due to the complexity of artwork preparation and the addition of many screens,typically ranging from 4 to 8. It is often used for printing complex images onto black-colored garments and can produce detailed, intricate imagery.
Please reach out for additional information on what may be best for your project.
LIMITATIONS & SIZING CONSIDERATIONS
-
8 colors/screens per garment
-
4 on tri-blends (3 on viscose blends)
-
7-8 on totes, depending on the graphic
PRINT SIZE
-
Standard: 14.5 " wide x 16.5 " tall.
-
Max height on an adult small pullover with kangaroo pocket: 10 " tall.
-
Max width on a youth small: 10.5 " wide.
-
For women and youth tees, 9 " wide is typical.
-
-
Toddler tee: 8 " x 7 " tall
-
Please note, we're not able to print on the sleeves of toddler long sleeved garments.
-
-
Pocket tee, or inside label graphic size: 2.6 " x 2.75 " tall.
-
Sleeve/Leg print: 3.5 " wide x 16 " tall.
-
Oversized (XL) screen max size: 14.5 " wide x 20 " tall.
-
Using XL screens is +$15/screen
-
-
XXL oversized screens (limited to 4 colors): 20 " wide x 28 ” tall
-
Using XXL screens is +$25/screen
-
Only fits for garments on sizes Large + up
-
This screen size is required for Bandanas typically
-
Standard print dimensions for our shirt screens are 11.5 " wide x 16.4 " tall, being the most ideal for making full use of a regular screen that can easily be streamlined from a unisex XS all the way up.
Please note: if the difference in sizes included in your order require us to rescale the size of your art, those items are invoiced as a different setup. Otherwise, all pieces will receive the same size print, and is printed according to the largest width that the smallest sized garment included will allow for.
For example, if you're looking to print the same graphic on toddler sized garments and also larger adult garments, you'll want to consider the print at two different sizes/setups;- the print scaled smaller for the toddler pieces, and separately scaled larger for the adult pieces. This will require our minimum of 10 pieces for each setup to proceed.
TOTES
-
Tote bag must be minimum 10" wide. Print must be 2 " from all sides
-
Tote prints are setup separately from shirts, so if you're looking to include both on your order (even for same print design), you'll need to meet our minimum of 10 pieces/ea (10 shirts + 10 totes).
MINIMUM ORDER QUANTITY
-
The minimum quantity of garments for printing is 10 pieces per setup.
ARTWORK
-
We use 4 pixels of trapping on overlapping / butted up layers. White underbases are contracted by 4 pixels from the layer overprinting them.
-
Minimum detail retention for garments: 6 pixels at 600 DPI (3 pixels at 300 DPI).
-
For totes, this should be 10-12 pixels at 600 DPI (5-6 pixels at 300 DPI).
-
Please see Artwork page for further information.
INSIDE NECK LABELS
We typically tear out the manufactures label to make this location most accessible for best print results. This tear-away service incurs at 25¢ charge per item. Please check to confirm if the garment style for this removal service includes a 'Tear-away' type tag.
Because of this, any inside print should also include more or less the same info as the manufactured tag, with the minimum being the:
- Garment size
- Manufactured country of origin
- Fabric content
- Garment RN# (need help with this? Let us know, we'd be happy to assist)
- RN is imported goods identification number that we're required to abide by for resale.
- Optional: Care instructions
We ask that all the required information above is provided in the inside label graphic intended for print. If additional information needs to be included, we can assist, but this may incur an additional art fee.
Please note: we require an average of 10 pieces per size if printing inside neck labels; maxed out at a 75/25 split. For example, 5 smalls and 15 mediums would qualify. This is applicable across multiple jobs.
It's recommend to print this location in a middle-ground color like light grey over black or white. In our experience, this middle tone yeilds a lower contrast that tends to look best, since it additionally prevents anything from being seen through the outside/back of the shirt.
FINISHING SERVICES
- We can fold and bag your garments using our compostable garment bags. This is an additional 50¢ per item and includes a size sticker on the outside of the bag.
FAQ
Will light ink on my dark garment show up?
Light Colored inks (excluding white) will darken up on darker fabrics. We can use a white underbase underneath these colors to help with the opacity. This is charged as another color in your design, if white isn't already being used in your print.
See example below:
What is the advantage of plastisol ink?
We use plastisol inks standard for our garment jobs, and it is phthalate free and baby safe! Plastisol ink offers brighter prints that last through many many washes.
What is the advantage of waterbased ink?
Waterbased inks are much more transparent than the standard plastisol, by nature. The result is a much softer print, that is ecofriendly. Recommended for darker colored inks on lighter colored tees; example black ink on a tan tee. Waterbased inks are and additional $0.25 per shirt, per color and are applied by request.
What are discharge inks?
Discharge inks are "water based" in a sense, but they react with the shirt fibers more like a bleach would, dying the garment back to its orginal color before it was dyed at a factory. Because of this, Discharge prints will look different from color to color, and even sometimes from shirt to shirt of the same color. A standard Discharge on a black tee, for example, looks like a light tan. The benefit of Discharge inks is that they are soft to the touch (not a thick, rough patch of ink) and they more opaque than regular waterbased inks. Discharge inks can also have pigmented of any color added to them for a colorful print. Please note, discharge printing is only available on 100% cotton shirts.
Can you print metallic ink?
The common metallic inks we use are Gold and Silver. Due to the lower viscosity and large metallic flakes in these inks, tiny details such as small text and halftone do not up hold well. To combat this issue we use a coarse mesh screen to acheive a clean, metallic print, which requires art to be 11-12 pixels @ 600dpi, vs. the required 6 pixels @ 600dpi for non-metallic inks. This applies to both positive and negative art elements.
Can I break my order into different colors & sizes of shirts?
Yes, but we ask that you keep the number of different items within a job within reason. A good rule of thumb is that you should have at least 3 items of any size/color combination. You can also print in one color on part of your order and another for a rest if there is at least 10 garments per color variation, however there is a $15 ink switch fee.